SURFACE HRD – QC
Quartz- and Corrunt-based Surface Hardener Mortar
DESCRIPTION
The product is a cement-based, high strength, microfiber-reinforced, ready for use surface hardening material containing quartz and corrunt aggregates of a special particle size and chemical additives enhancing product performance, which is applied through spreading in the form of powder on freshly finished floor concrete that would experience medium loads.
TECHNICAL SPECIFICATIONS
Appearance | Grey powder |
Amount of Consumption | 6-7 kg/m2 |
Application Temperature | +5 oC to +35 oC |
Time Before Walk on: | 24 hours |
Heavy traffic | 48 hours |
Toxicity | Non-toxic |
Pressure Strength | 80-85 N/mm2 (28 days) |
Wear Resistance | 7.8 cm3 / 50 cm2 (böhme method) |
* The above values are valid for + 23oC and 50% relative humidity. The time is shortened at high temperatures and extended at low temperatures. |
AREAS OF USE
It can be used safely on the floors of industrial plants, garages and parking lots, hangars and mechanical workshops, fuel stations, and warehouses.
BENEFITS
Thanks to its content of special chemical additives, it absorbs the water content of the floor concrete on which it is applied, and establishes a single structure with concrete after completion of finishing process. It is 2-4 times more resistant to abrasion than normal concrete surface. It has high adhesion ability. It is resistant to frost-thaw cycle.
INSTRUCTIONS FOR USE
The application of the surface hardener is intended to increase the abrasion, dusting, and impact strengths of concrete and screed on the upper part of concrete, and has no effect on the pressure, tensile, and bending strengths of concrete. Any incorrect projection defects as well as application cracks that may occur in the screed concrete would be entirely reflected on the surface hardener. After cleaning of the concrete surface to be applied with the surface hardener, the floating and monolithic screed applications should be selected based on project requirements. The surface should be roughened and the cement slurry should be removed. The existing concrete surface must be saturated with water at least one day before the application starts and there should be no free water left on the surface. The jigs are placed according to the project. Before starting the spreading application, the concrete with a triangular cross-section in dimensions of 5x 5 cm should be removed using a trowel along the joint by the edge of the jig. EKOKAT SURFACE HRD - QC surface hardener with a thick consistency should be applied with a trowel into the location of the concrete removed as such. This will prevent the joint edges from breaking under load. It must not be spread from far distances when applied in order to prevent the aggregates contained in the surface hardener from dissolving. The spreading application should be carried out after completion of the hardening process so that a footprint with a depth of 0.5 - 1.5 cm is left when concrete is pressed depending upon ambient and weather conditions. The product should be sprayed and smoothed as homogeneously as possible. First, 2/3 of the total consumption amount is spread on the concrete surface and spread by machine. The spread material should be allowed to get dampened by absorbing water out of concrete, and the surface hardeners should be integrated to the concrete through the application of a disk finishing process. Then the remaining material should be spread on the concrete surface as in the first application and the same works should be repeated. A fine finishing process should be applied after completion of the rough finishing process. The fine finishing is the one that is performed with a knife. The finishing process with a knife should be done until the desired Brightness is achieved. After the application of the surface hardener is completed, the surface is cured so as to prevent shrinkage cracks and to provide a dust-free medium. The curing process should be done certainly in the summer and winter. After the application is completed, the joints of the jigs should be cut with a width of at least 4 mm in order to form joints. Joints should be filled with a suitable mastic.
PACKAGING
25 kg PE reinforced craft bags
64 shrink bags on one palette (110x110 cm).
STORAGE CONDITIONS AND SHELF LIFE
No more than two palettes should be placed on top of each other in their unopened original packaging, in a cool and dry environment. Shelf life is 12 months from date of production under suitable storage conditions.
SAFETY MEASURES
Work clothes, protective gloves, goggles, and masks suitable for workers health and safety should be used during the application. Due to irritant effects of uncured material, it should be washed with plenty of water and soap immediately in case of contact with skin and eyes. If swallowed, seek medical advice immediately. No food and drink should be brought into application areas. Store it out of reach of children. Please refer to the safety data sheet for further information.
RESPONSIBILITY
Our Company may not be held liable for any application errors that might be suffered if the product is not used for its intended purposes, or if it is failed to conform to the conditions and proposals specified above regarding technical application. This technical data sheet contains information that is current as of the date of issuance hereof. The manufacturer hereby reserves its right to change this data sheet at any time.
- EK 1020.010.25
- Grey
- EK 1021.030.25
- Red
- EK 1022.040.25
- Yellow
- EK 1023.050.25
- Green
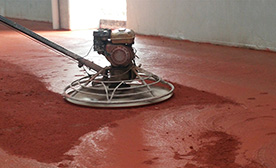
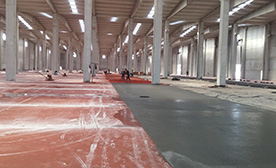